Hybrid Systems in Mobile Applications
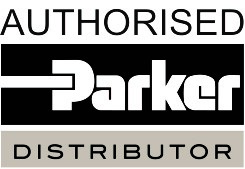
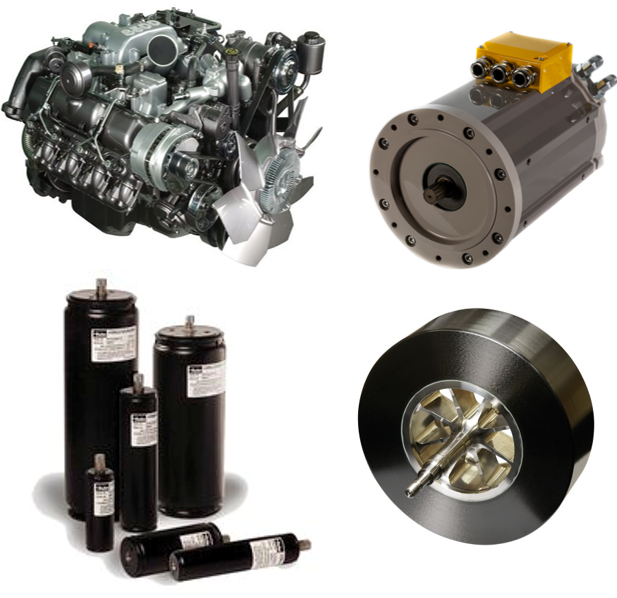
A hybrid system, specifically a hybrid system, uses at least 2 energy sources to power a vehicle. The most common source is the electric hybrid, which means, in addition to fuel in the ICE (Internal Combustion Engine), electric power is stored in a battery or supercapacitors to help power the application. The electric system is very interesting because it allows you to store energy for a long time using the electric motor as a generator.
Hybrid systems can also use hydraulic accumulators, while other systems are based on KERS (Kinetic Energy Recovery System). KERS is a mechanical energy storage system based on a flywheel, that can also be considered an energy source.
Hybrid systems cover a wide range of different technologies, however, this presentation will focus on electric hybrid technology.
– System that uses 2 energy sources to power a vehicle
– Potential energy sources
– Diesel (ICE)
– Electric (M/G)
– Hydraulic (accumulators)
– Mechanic (KERS)
– Typically use hydraulic accumulators
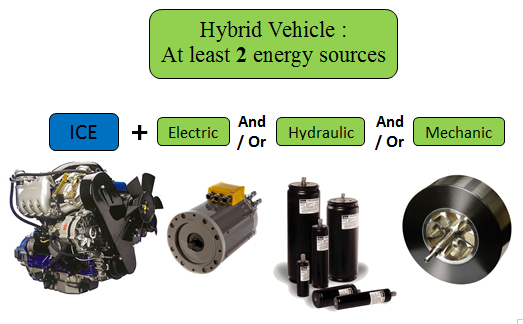
There are many benefits associated with hybrid vehicles including, fuel savings, reduced emissions, and ICE size reduction. To reduce fuel consumption, the hybrid vehicle stores electric energy to work with the ICE, so that the engine is not the only energy source. Fuel consumption reduction directly leads to emission reduction, which is becoming a crucial feature as there are more and more CO2 and Nox levels of emission restriction being put into place. Lastly, as electric energy is used, it reduces the ICE required power. As a result, the ICE size can be reduced. A potential disadvantages is that the electric system requires a bigger initial investment.
Hybrid Vehicle Benefits:
– Fuel savings
– Reduced emissions
– Compliance with new directives
– Euro 6 for commercial vehicles
– Stage IV for mobile machinery
– ICE size reduction
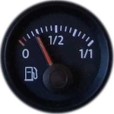
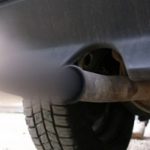

Applications
With the hybrid concept, when a vehicle brakes, it allows the engine to recharge the battery instead of loosing energy through the mechanical brakes. This concept applies to all vehicles including commercial and personal vehicles such as cars and motorcycles. The same concept includes man lifts and reach stackers as it allows these applications to avoid ICE idling periods where full power is not required. This concept however, does not apply to trucks that have a longer travel distance or any vehicle which ICE is consistently running at a high power level.
There are many hybrid vehicles including:
– Motorbikes and Scooters
– Automotive
– Commercial vehicles
– Bus and Coaches
– Construction vehicles
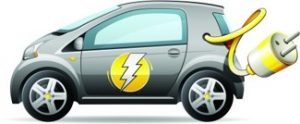
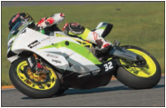
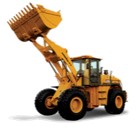
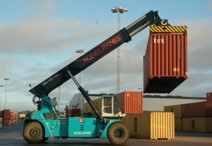
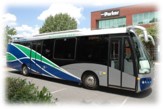
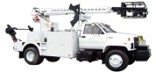
Hybrid Parallel Systems
In a hybrid parallel design, both prime movers, the ICE and the electric motor, are physically connected to the vehicle’s wheels as if they were “parallel supplies”. The electric motor is directly linked to the wheels and the battery cannot be recharged if the vehicle is not moving. As long as the vehicle is moving, the BMS (battery management system) has to decide if the electric system is used as a Motor or as a Generator. This kind of Parallel Hybrid system is typically used as it does not require big mechanical modifications on the vehicle frame to go from a 100% ICE power to a Hybrid power. The clutch enable the ICE to be stopped when it is not required.
For the same power, the ICE size is reduced next to the electric assistance.
First Hybrid Parallel Type:
– Internal Combustion Engine and Traction motor /generator is in line with one another and rotates at the same (low) speed
– Transmission is a gearbox
– The generator can recharge the battery when braking, even if ICE is stopped and the clutch is open
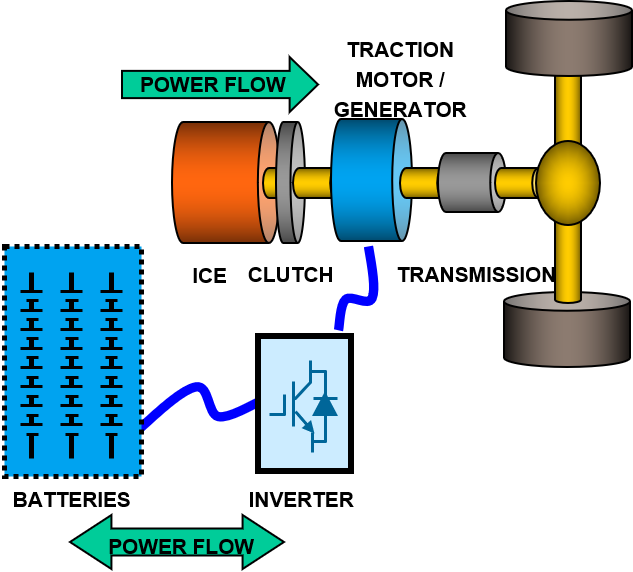
Parallel Hybrid Electric Architecture / Example
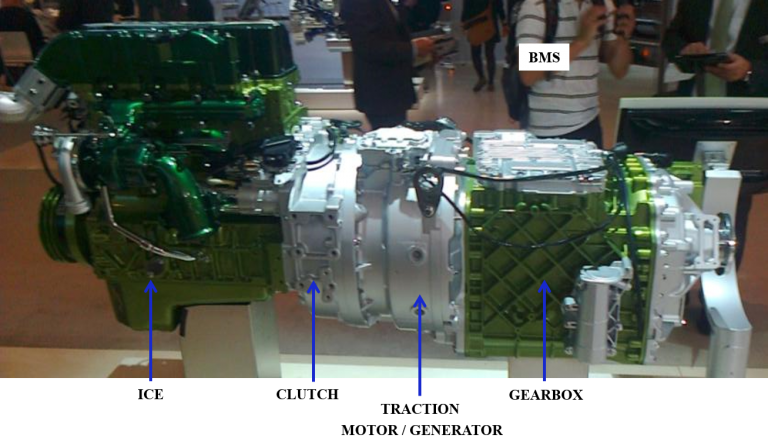
Hybrid Parallel Systems
In this parallel hybrid configuration, the ICE and electric motor/generator can be independently sized for the vehicle to be well adapted for the area where it will be used. This configuration is mainly used on city busses as it tends to be more mechanically complex, requiring a specific transmission. This configuration can be considered as the future of parallel hybrid systems.
Second Hybrid Parallel Type:
– Traction motor /generator is linked to the wheels through a constant gear ratio
– Electric motor and ICE can be sized independently one from the other
– This configuration requires a heavier vehicle frame modification
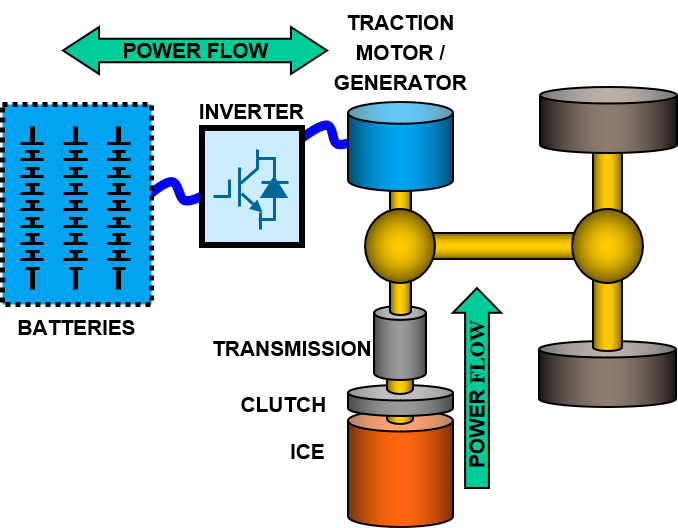
The electric hybrid parallel bus starting system is typically used on city buses as they can globally recover a large amount of energy. When the bus is stopped and people are getting in the vehicle, everything is stopped and there is no movement either on ICE or electric motor. When the bus leaves the bus-stop, the clutch is opened so that the ICE is not needed and only the electric motor moves the bus using the electric power stored in the battery.
Example: Bus electric starting
– ICE stopped
– Clutch opened
– Vehicle starting only on battery power
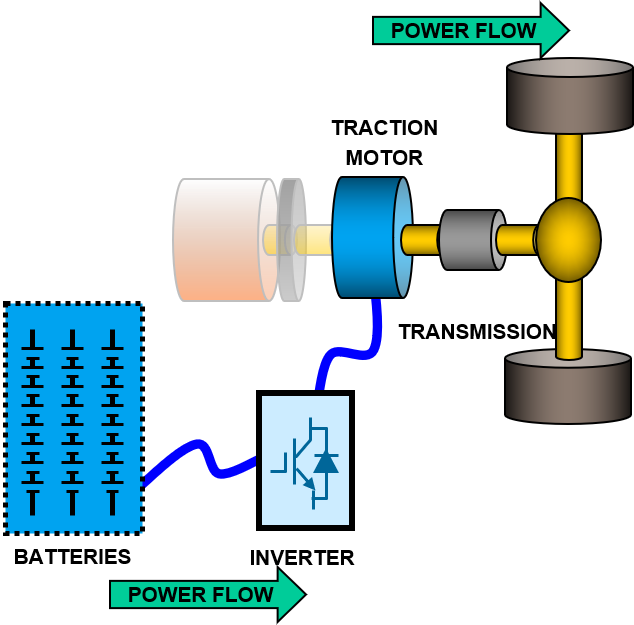
When the bus exceeds 25 km/h, the battery plus the electric motor power is no longer sufficient to accelerate the vehicle. At this point, the ICE is started and the clutch is closed for both diesel and electric motors to provide global high level traction power.
Example: Bus Hybrid Cruising
– ICE is started
– Clutch is closed
– Vehicle is cruising on diesel and battery power
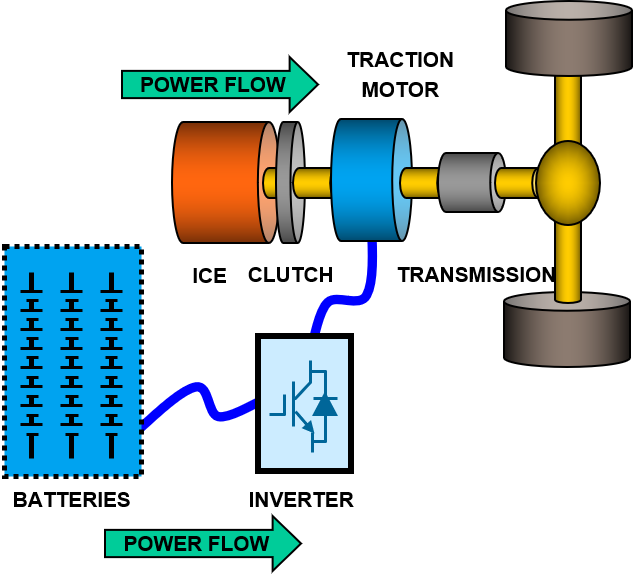
While cruising, if the BMS (Battery Management System) supervising the electric system detects a low battery, the electric motor is used as a generator to recharge the battery through the inverter in the regenerative mode.
Typical Battery Recharge Mode:
– ICE is started
– Clutch is closed
– Electric motor used as a Generator
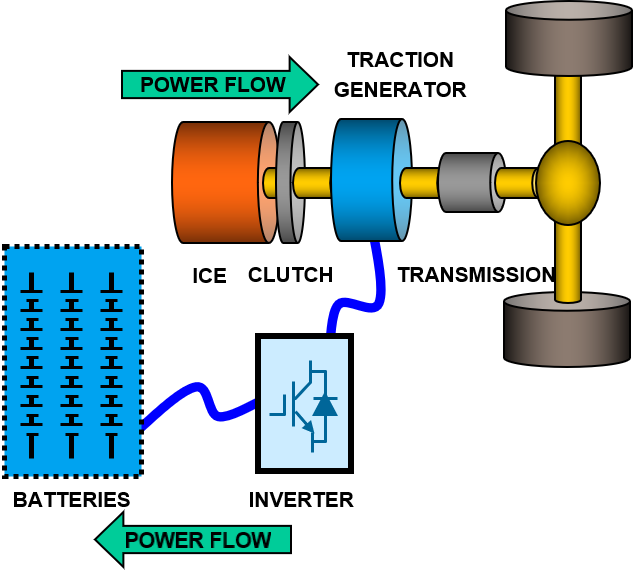
When the bus gets to the next bus-stop, the cluth is opened, the ICE is stopped and all the kinetic energy is recovered in the battery through the electric motor used as a generator. This kind of hybrid configuration allows energy savings of over 35%.
Typical Regenerative Braking:
– ICE is stopped
– Clutch is opened
– Electric motor is used as a Generator
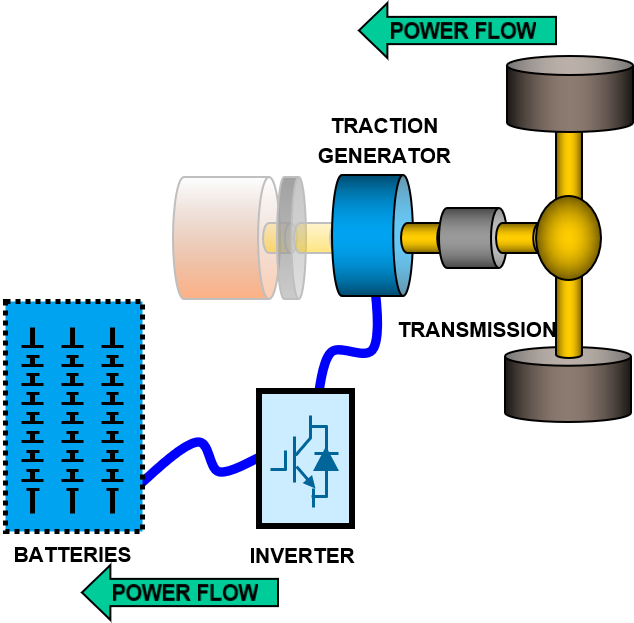
Hybrid Series Systems
Series hybrid systems are built around a battery that is charged through an ICE connected to an electric generator. The ICE is used at its more efficient rotation speed and the efficiency level of the generator is also very important. The electric power is then used for traction or any system based on electric power (EHP (Electro Hydraulic Pumps) for example). As a result, the hybrid series system can be considered a very flexible system, even if its only for traction. The hybrid series energy saving level (around 30%) is a bit lower than with the parallel hybrid one.
Hybrid Series System:
– Internal Combustion Engine provides electric power through a generator
– No mechanical connection between the ICE and the wheels
– Electric motor is the only one to be used for traction in this example
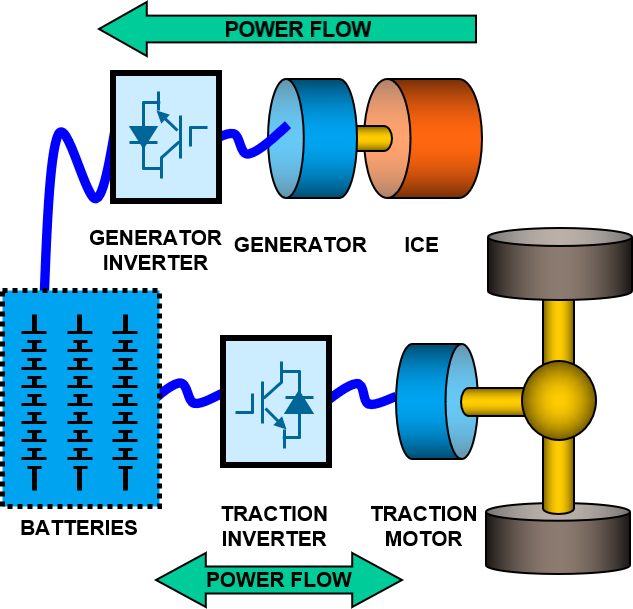
When starting the vehicle, the electric motor is used based on the electric power available from the battery charge level which is supervised by the BMS (Battery Management System). Depending on the required performance, a gearbox may not be mandatory. In this case, the electric motor can be used with a fixed gear ratio.
Example: Typical Bus Electric Starting:
– Internal Combustion Engine provides electric power through a generator
– Electric motor is using the available electric power provided by the battery
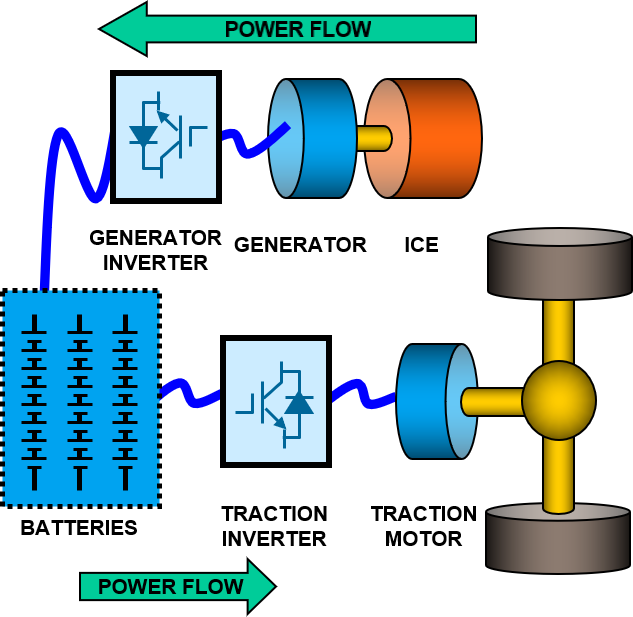
At this state, the electric traction motor is used as a generator while decelerating or braking, so that the battery is recharged through both sides. The main benefit of this system is, by rotation speed and averaging the power requirements through the battery, the ICE size can be reduced.
Typical Regenerative Braking:
– ICE still provide electric power to the battery
– Electric motor also used as a Generator
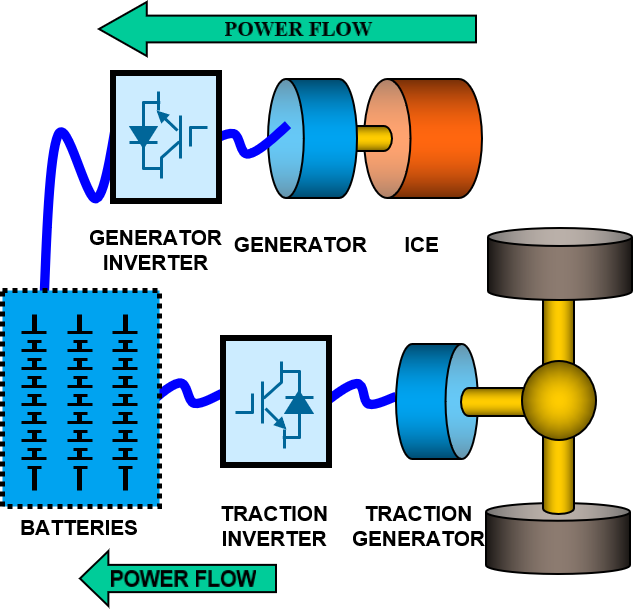
Series Hybrid Electric Architecture / Example
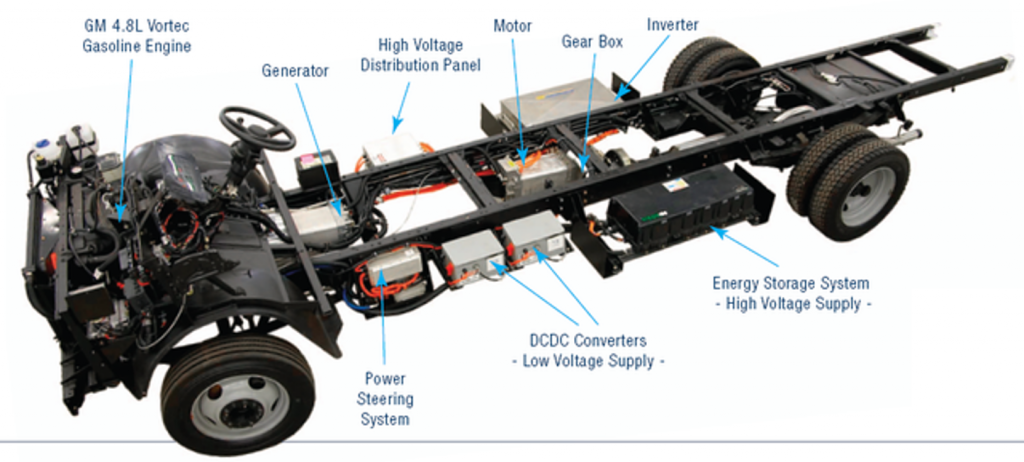
Hybrid Electric Technology:
Hybrid electric technology is becoming very popular and vehicles manufacturers will have to start developing products that use this technology before moving towards 100% electric vehicles. At the moment, more and more questions are being raised about this technology and many companies are looking for the best solution depending on their project. Also, due to environmental reasons, there are more low emission zones being created in major cities, along with restrictions about polution, noise and more that will lead to a global need for hybrid electric technology.
Hybrid Electric Technology:
– More vehicle manufacturers are interested in hybrid electric technology
– More end users are required to comply with emission requirements
– More restrictions on emissions, and noise
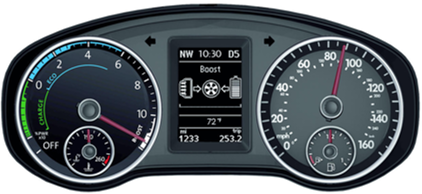